In Switzerland, Bell relies on the services of railCare AG, a wholly owned subsidiary of Coop. coop took over railCare AG in 2010. It was only with this collaboration and the resulting opportunities that Bell Logistics was able to embark on such a relocation project. The biggest challenge and a key criterion for a successful changeover is the functioning of the order-delivery rhythm.
Sustainably combined
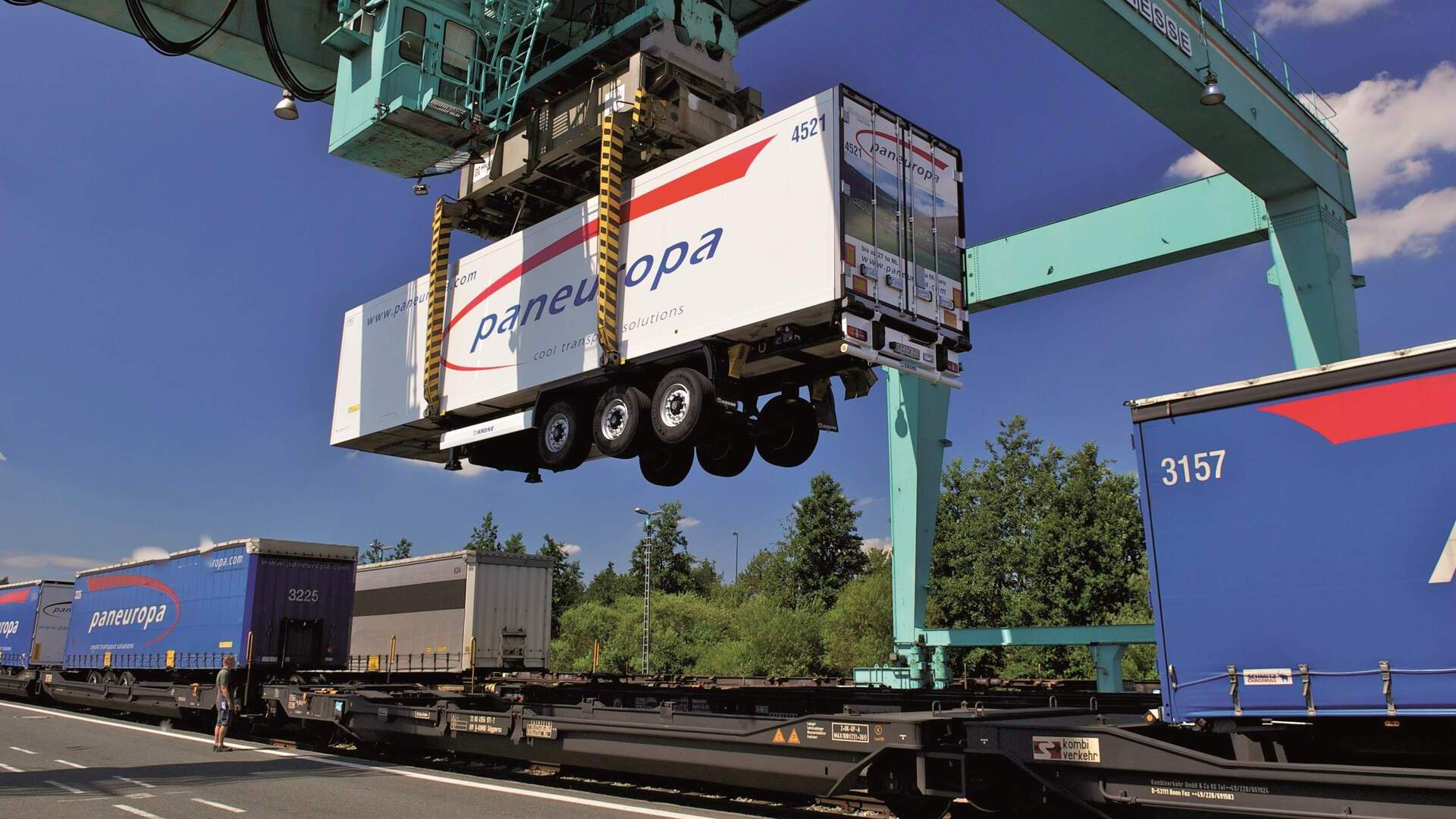
The Bell Food Group (then Bell Group) sold 275,000 tons in 2015. However, all of this had to be transported first, from the affiliated companies and factories via distribution centers to the stores and customers. Behind this is a sophisticated piece of machinery: logistics. With these enormous quantities, it is clear that sustainability considerations and measures play an important role in transportation and distribution. An important piece of the puzzle here is the switch to combined transport, the transfer of transportation from road to rail.
In Switzerland, products have been transported from Basel, Oensingen and Cheseaux to Ticino by combined transport since 2013. Thomas Abt, Head of Logistics at Bell Switzerland, explains the sustainable goals behind this project: "We care about the environment and use our resources carefully. We want to avoid unnecessary transports, use vehicles that are fully utilized and thus reduce CO2 consumption."

"If the train leaves on time at 8 p.m., the products must also be delivered on time for loading in advance," explains Thomas Abt. He compares this to a clockwork mechanism in which the gears have to mesh perfectly. The products from Basel are transported by truck from the charcuterie, fresh meat and seafood plants to the railCare hub in Oensingen. Products from the plant in Oensingen and from Cheseaux also arrive at this hub. Packed in swap bodies, everything is then loaded onto the rails and transported to the Castione hub in Ticino. There, the onward transportation to the customer, the so-called last mile, is again carried out by truck. "The order-delivery rhythm for combined transport has worked very well so far and also has potential for more," says Thomas Abt

A very similar relocation project was also implemented at Bell Germany in 2016: Prosciutto is refined in Italy and further processed at Bell's own Harkebrügge slice center in northern Germany. Until then, the goods were collected from the manufacturer in Italy in a refrigerated truck. Today, however, the truck does not travel directly to the north, but to the loading station in Verona. There, the complete refrigerated trailer is placed on a wagon, which is part of the freight forwarder's block train. This block train reaches its destination station in Bremen within 24 hours. From there, the refrigerated trailer is transported back to Harkebrügge by road.
Both projects showed remarkable results: Bell Germany was able to achieve 70 percent lower CO2 emissions and also reduce costs. The Swiss example even allowed a saving of 85 percent, which corresponds to 156 tons of CO2.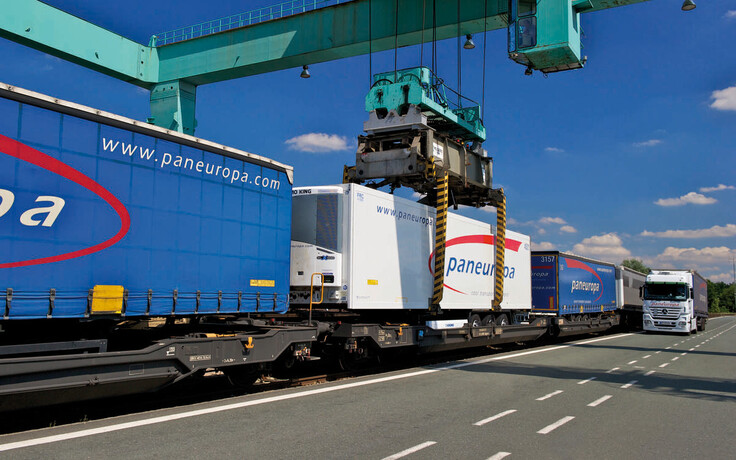